Why use high pressure reactor ?
For the efficient synthesis of novel molecules, materials and polymers scientists employ a broad range of experimental techniques and equipment. Reactions carried out at very low temperature under an inert atmosphere at high dilution can usually be performed in a conventional round bottom flask whereas reactions that require elevated temperature and high pressure need to be carried out in a specially designed high pressure reactor.
A high pressure reactor can offer several advantages over a conventional round bottom flask for conducting chemical reactions. It enables reactions to be carried out under elevated pressure and at temperatures higher than the boiling point of the reaction solvent or solvent mixture. These factors can lead to a significant increase in reaction rate to produce the desired product and thereby minimise the decomposition of substrates and/or products leading to a cleaner reaction profile.
Why it is essential to use a suitable pressure reactor ?
Carrying out a reaction under pressure in a suitably designed reactor, can lead to an increase in the safety of a procedure by containing potentially toxic materials or gases in a controlled environment.
Not all commercial high pressure reactors are the same, they differ considerably in their quality of construction, safety features, ease of set-up and use, ease of maintenance and versatility to handle different corrosive materials and reactants under high pressure
Why was the PressureSyn developed ?
In the School of Chemistry at the University of Nottingham (UK), one area of specialism is the use of supercritical fluids, such as carbon dioxide, as a “green” solvent for polymer synthesis and materials processing. This research is led by Prof Steven Howdle and his group required access to equipment which would enable the development of efficient synthetic protocols for the preparation and isolation of a variety of polymeric materials quickly, easily and most importantly, given that the reactions would be carried out at elevated temperatures and high pressures, in a safe manner. The group investigated a number of high pressure reactors which were commercially available at the time however they did not meet the groups’ requirements in terms of ease of set-up, operation, cleaning, versatility of use and safety.
Driven by their desire for an affordable high pressure reactor that combined ease-of-use, outstanding performance, ease of maintenance and high operational safety, Professor Howdle embarked on a project with colleagues Martin Dellar, Peter Fields and Richard Wilson based in the University’s workshops, to design and develop a bespoke high pressure reactor. Asynt Ltd collarorated on the project.
What are the innovant specifications of the PressureSyn, why is it a unique product ?
The design of the PressureSyn
A major design feature introduced into the new reactor was a novel clamp. This is used to fasten the body of the reactor to the head piece which contains valves to allow the introduction of reagents and gases as well as monitoring the pressure and temperature of the reaction. A clamp design to secure the body to the head was favoured rather than use of a screw thread, as in the latter, there is the possibility of cross threading and accumulation of materials in the screw path required to join the sections together.
One potential safety issue which had been identified in a clamp design was the possibility of opening the reactor whilst still under pressure when undoing the clamp. When a regular high pressure valve is opened at the end of the reaction, it could be assumed that the pressure has been released. However it is possible to have a small blockage in a valve leading to some residual pressure. If the clamp was removed under such conditions, the head metal could have sufficient momentum to fly off and potentially cause serious injury to the scientist. This required a safety design feature to be developed for the new reactor to ensure that all residual pressure was always released.

Fig 1. PressureSyn safety key
Nottingham engineers came up with a novel safety valve design. At the end of the reaction, after the pressure had been released and the pressure gauge read zero, a valve could be removed to leave behind a hole of a few millimetres in diameter ensuring any residual pressure would be released.
A further safety feature was that the head of the safety valve also operated as the key which had to be physically inserted into the clamp to undo and remove it. Therefore it would not be possible to manipulate the clamp in any way without firstly removing the safety key and hence releasing any unexpected residual pressure in the reactor.
This simple yet highly effective safety feature, inherent in the design of the new reactor is shown in Figure 1.
Each key in the new design is individually engineered to fit only one clamp therefore it is not possible to undo the clamp using another key whilst there is the possibility of the reactor being under pressure. In order to ensure that the clamp did not introduce areas of stress into the body of the reactor, measurements were made of the complete assembly. As shown in Figure 2 there are no significant stress seen in the area where the clamp is fixed onto the reactor body.
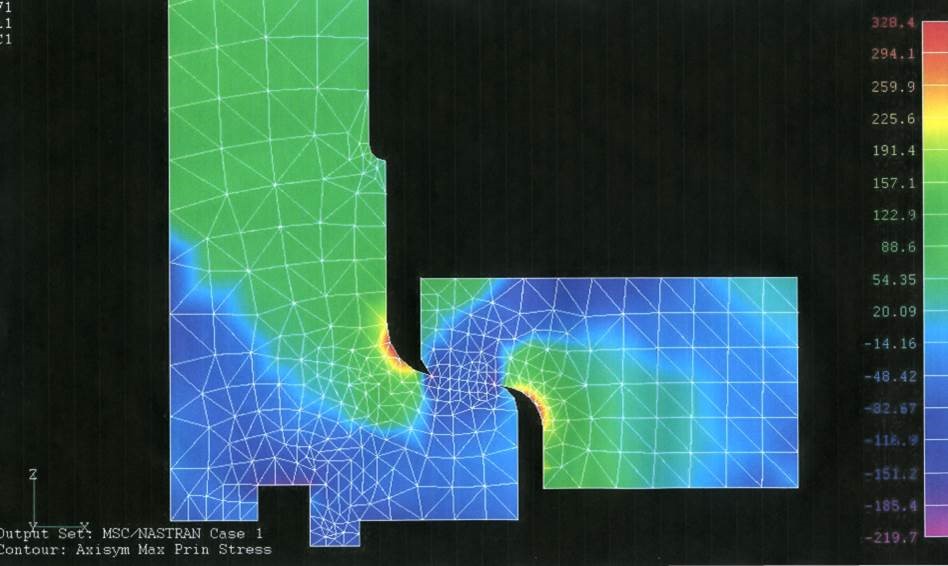
Fig 2. Stress measurement patterns on PressureSyn reactor body
The reactor head of the PressureSyn
The flexibility of the design enables the PressureSyn reactor be utilised in a wide range of high pressure reactions. The reactor head is fitted with a number of ports including pressure gauge, pressure relief valve/bursting disk safety features, outlet valve, thermocouple, gas inlet value and safety valve. As an alternative configuration, replacement of the gas inlet valve with a blanking valve would allow the PressureSyn to be utilised as a standard autoclave.
The material used for PressureSyn reactors
PressureSyn reactors are produced as standard in durable SS316 stainless steel however the same design can be used to manufacture units in acid resistant alloys such as Hasteloy. The reactor can be fitted with a magnetic stirrer bar and used in collaboration with a metal heating jacket and placed on a stirrer hotplate as shown in Figure 3. The specification of the reactor enables reactions to be performed up to maximum working pressure of 100barg @200°C.
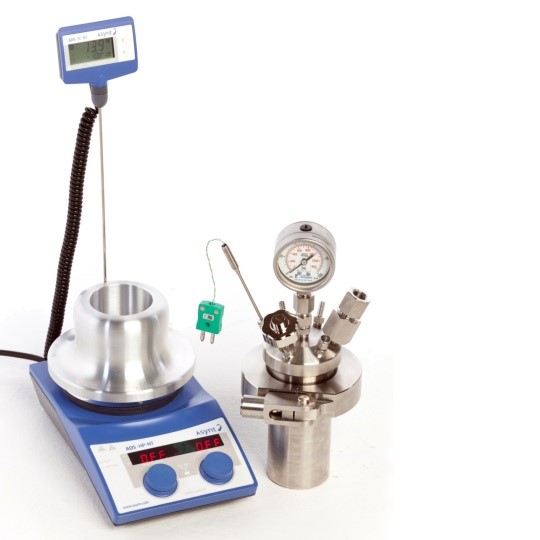
Fig 3. PressureSyn Reactor on stirrer hotplate
Warranty as what the PressuSyn is a really reliable
To ensure the operational integrity of the new design, the PressureSyn reactors have been extensively tested and used by various research groups in the School of Chemistry at the University of Nottingham. Using a wide range of standard operating procedures developed for specific experimental conditions there have been no safety incidents reported, which proves testament to the safety key design.
Conclusions
The PressureSyn is eminently suited is in homogeneous or heterogeneous reactions which require a gas at higher than atmospheric pressure and high temperature. Its reactor, with the incorporation of a unique safety key concept, developed by scientists and engineers, has enabled a variety of novel research approaches at elevated temperatures and high pressures to be undertaken in a safe and efficient manner. The PressureSyn leds the users to produce significant improvements in applied materials research, production of commercially important polymeric materials and have impacted significantly in the area of healthcare.
To know more :
For further information please visit our web site
Litterature, application
A variety of reactions carried out in the PressureSyn reactor have been reported in the literature :
Ref 1: Busby, A. J.; Zhang, J.; Naylor, A.; Roberts, C. J.; Davies, M. C.; Tendler, S. J. B.; Howdle, S. M. J. Mater. Chem. 2003, 13 (11), 2838-2844
Ref 2: Maria del Carmen Gimenez-Lopez, Alessandro La Torre, Michael W. Fay, Paul D. Brown, and Andrei N. Khlobystov, Angew. Chem. Int. Ed. 2013, 52, 2051 –2054
In a recent publication by Howdle et al (J. Am. Chem. Soc. 2012, 134, 4772-4781) work towards the synthesis of structured block copolymers which are important in myriad applications from catalyst supports to data storage was reported.
Using the PressureSyn reactor, Prof Howdle developed a new reliable and controllable route via reversible addition-fragmentation chain transfer (RAFT) dispersion polymerisation in supercritical CO2 to give access to these materials in a versatile one-pot process.